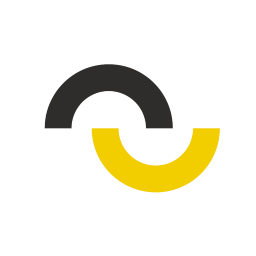
There are many challenges facing those in the food and beverage industry right now. Whether that may be overstocking of some items that are not selling, shortages of others as they may be difficult to source, or indeed a complete removal of some lines as the supplier is in difficulty.
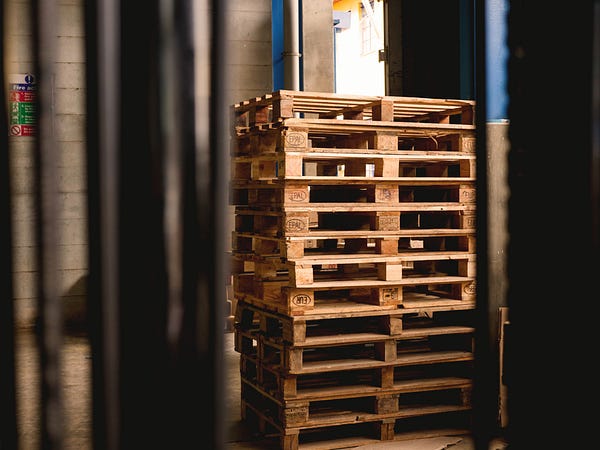
As government and management-mandated shutdowns increase, and fewer and fewer employees are able to come to work, your company may face a wide range of supply chain challenges. Your own production and ability to supply customers may be affected, or you may be unable to produce your goods because your suppliers have discontinued shipments.
Is your stock management system letting you down? Smarter in-house management of stock is one of the first things to look at to ensure you are working with real-time statistics that show exactly what items are needed and what you already have enough of.
If you are in the position of potential wastage happening due to short dates on produce, consider ways in which you can help your local community right now. Moving smartly here will free up valuable warehouse space for those products you need to stock more urgently.
Without criticism, this is probably an excellent time to be learning lessons about how your organisation works in a crisis situation. Many of us haven’t been in a situation like this in our lives before, and I’m sure that the tenacity and resilience of many businesses and supply chains have been tested to the maximum.
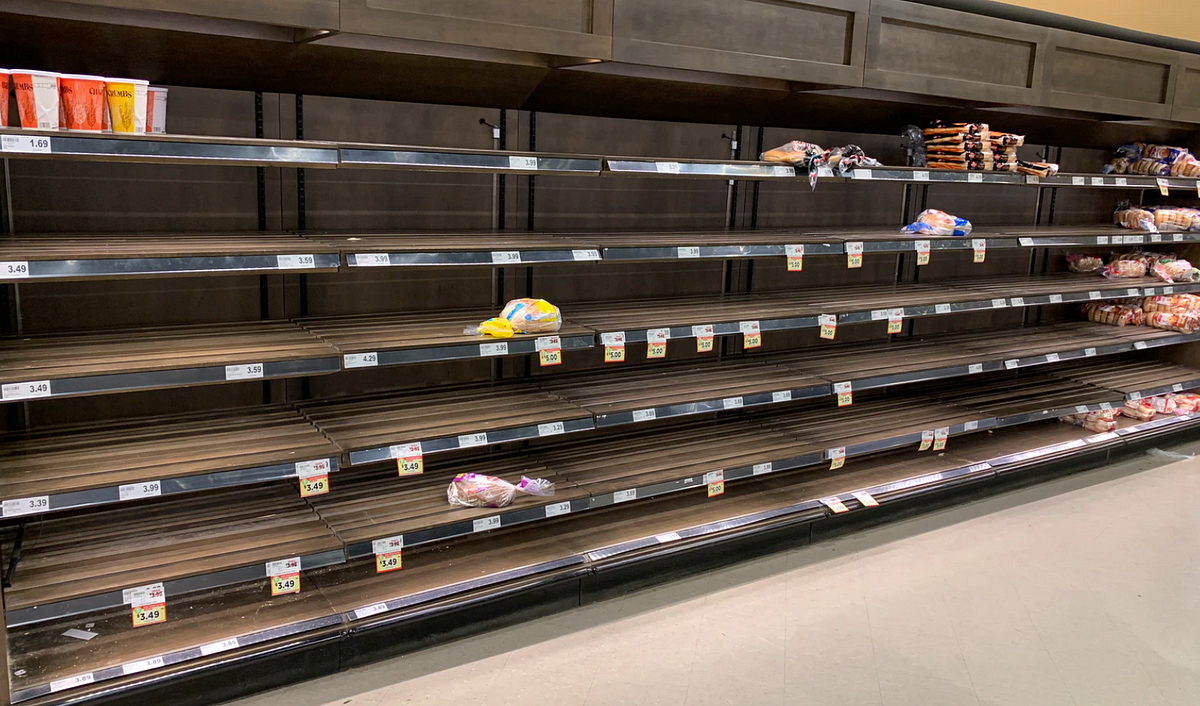
Are there areas that have been a success or indeed others where costs have risen due to having to source more products quickly? Which part of your supply chain worked well and which could do with improvement? Ensuring this feedback process takes place will help a busy food warehouse to work optimally and is a good exercise in risk management for the future.